Perfect Performance
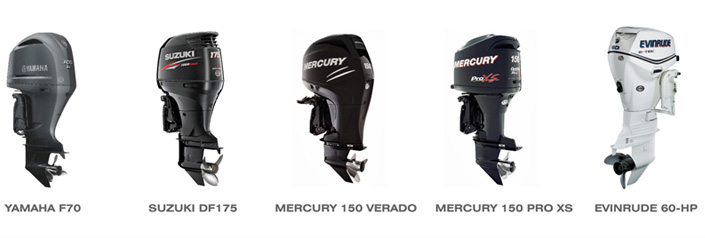
In the highly competitive world of outboard engines, manufacturers strive for the lightest, most efficient and powerful design.
Hidden beneath a solid-colored cowling and simple decals, the outboard engine can be overlooked by casual boaters, who may be more impressed with a booming sound system or onboard wet bar.
But for the performance-minded, there is beauty in the mechanical orchestra below, which can deliver scorching holeshots and responsive acceleration while maximizing fuel efficiency and comfort.
Technological evolution in outboard engines happens rapidly. By responding to ever-changing consumer demands, today’s manufacturers are producing fine-tuned excellence, whether the technology is four-stroke or two-stroke, direct-injection.
To identify the latest advancements, Boating Industry spoke with major manufacturers in both segments of today’s outboard industry.
Four-stroke
With the majority of outboard manufacturers focusing on four-stroke engines exclusively, the sector is extremely competitive. Each player works tirelessly to create the lightest, most efficient and most reliable outboard engine in all horsepower ranges.
With the rising costs of fuel, some manufacturers have seen increased demand for smaller engines. Today, the best sellers are midrange outboards, which have benefitted from many new technologies previously reserved for their high-performance, high-horsepower counterparts.
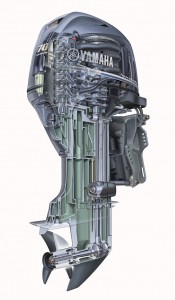
Yamaha’s newly released F70 midrange model incorporates four valves per cylinder into the engine. The design gives the outboard better acceleration by efficiently utilizing its displacement. By using a single overhead camshaft, a low weight was also maintained, according to Ben Speciale, president of Yamaha Marine Group.
In 2011, Suzuki Motor Corp. received an NMMA Innovation Award for the DF40/50-horsepower midrange line, after the manufacturer began integrating larger engine features like dual overhead cams, digital fuel injection and its Lean Burn technology into lower horsepower engines.
“We are not saving all of the wazoo stuff for the big engines,” said Gus Blakely, sales manager at Suzuki. “The small and midrange outboards also benefit from these improvements.”
Weight reduction
No matter the horsepower, customers expect excellent acceleration at all RPM ranges, and manufacturers are accomplishing this by creatively maximizing displacement while minimizing weight.
Speciale said Yamaha’s 4.2-liter outboards utilize plasma-fused cylinders, which remove the steel sleeve and use a plasma-fused coating on the cylinder walls. This achieves an improved power-to-weight ratio by reducing the weight of the cylinder block and adding displacement.
“I expect to see a lot more innovation in that power-to-weight area as technology advances in materials, processes and alloys,” Speciale said.
At the 2012 Miami International Boat Show, Suzuki brought prototypes of what these future materials could be. A tiller handle made out of magnesium, which is lighter than aluminum or steel, was shown to customers. Unfortunately, magnesium is also corrosive, so Blakely said protective coatings would first need to be developed before the material could be used. Suzuki also displayed a couple of engine cowlings made of carbon fiber, an aerospace-type product with weight advantages over fiberglass.
“We can reduce the weight but still maintain that strength and rigidity,” he said. “But the final product has to be affordable, or it cannot be put on the production line. Nobody is going to pay a zillion dollars for an outboard motor.”
Maximizing efficiency
Weight reduction is vital for fuel efficiency, but it is only one method manufacturers use to attain superior performance economically.
In 2007, as part of its second generation of Verado outboards, Mercury Marine did a massive internal friction reduction on the engine line. The result was significantly increased fuel efficiency by reducing the amount of oil that remains suspended whirling around the crankcase, said Steve Miller, senior category manager at Mercury Marine.
Miller said Mercury also focuses on minimizing parts wherever possible without sacrificing reliability or performance. For example, when other manufacturers continued to advertise using four valves per cylinder to gain power, Miller said Mercury is delivering comparable or better performance with less weight and smaller package size using two-valve heads on its newest models.
“One of the things we have learned is that you can develop great performance out of a two-valve head without that added weight and mass,” he said.
While Suzuki is migrating many of its technologies down to its smaller engines, Blakely said this mindset is different when it comes to the number of cylinders. On its DF150 and DF175 models, Suzuki aimed to provide V6-like performance with a four-cylinder outboard while utilizing a dual overhead camshaft configuration, along with direct fuel injection and an offset drive shaft.
“We listened to our customers and made an outboard that was lighter and offered better fuel efficiency, all in a more compact design,” Blakely said. “There was an opportunity there for us to incorporate this technology, and it has been successful.”
ECUs
Many of these advancements would not be possible without major improvements in the engine control unit (ECU).
By controlling, among other things, fuel injection and air delivery into the engine, Yamaha’s Speciale said the ECU has had a tremendous effect on an engine’s power-to-weight ratio, with lighter engines delivering superior performance.
The ECU has also improved the experience at the helm, where boaters are treated with digital throttle and shift systems and a customizable interface displaying virtually limitless information originating with the control unit’s sensors.
“Years ago you just had your standard analog gauges. Now you can monitor your fuel efficiency and dial it in to maximize performance,” Mercury’s Miller said.
Released last year, Mercury’s ECO-Screen learns the customer’s boat operating patterns by monitoring fuel burn and trim angle, the goal being to assist the boater in finding the sweet spot that maximizes fuel economy, according to Miller.
The ECU allows boaters to use a digital shift and throttle system, like Suzuki’s Precision Control unit offered in its DF300 model. Replacing cables, the system erases the friction and resistance associated with shifting and throttling, creating positive, instantaneous and decisive control, according to Blakely.
Gear cases
Although not as flashy, the evolution of gear cases has been equally important to the performance and fuel economy of today’s outboard.
At Mercury, the gear cases have been given larger torpedoes to better lift heavier boats, while also becoming more hydrodynamically efficient.
“All the torque and horsepower within the engine, it is only as good as its ability to transition power to the water,” said Miller.
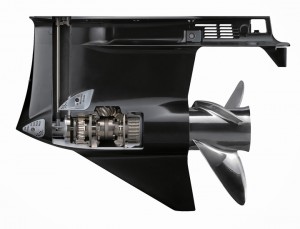
In 2012 with its DF300 model, Suzuki implemented Select Rotation, which allows boat builders and dealers to select between a standard and counter rotation lower unit. And with its introduction, Suzuki also created a gear case that was larger yet more efficient than its predecessor. With the high gear ratio of 2.08:1, Suzuki’s DF300 can use a 16-inch propeller, vastly improving holeshot and midrange performance.
“The big propeller, high gear ratio allowed us to get that holeshot in the midrange that was previously lacking in four-strokes,” Blakely said.
To further increase the propeller’s effectiveness, Blakely said Suzuki has also started exploring titanium for future models, which would allow for razor thin blades, reducing drag while maintaining strength.
Two-stroke
At Mercury Marine, the majority of outboard engines sold are four-stroke; however, the engine manufacturer’s two-stroke, direct-injection engines are popular with the bass market, due to the performance characteristics synonymous with a two-stroke engine.
“Those guys like the combination of acceleration and top speed, while being the right weight on a tourney-size bass hull,” Miller said. “They can run to the different spots and still make the road home for weigh-in.”
Two-stroke, direct-injection models like those offered by both Mercury and Evinrude have evolved to better utilize these inherent advantages.
Producing a power stroke with every revolution of the crankshaft, two-stroke motors generate max power over a wide range of RPMs.
To further take advantage, Evinrude uses a variable exhaust valve in its 115- and 130-horsepower models that changes the path length of the exhaust, manipulating the length to get the most power in a particular RPM range.
“It is why we are able to develop a V4 that makes a ton of horsepower at the top end, but incredible low-end power to get out of the hole,” said Karl Sandstrom, product manager at Evinrude.
For Evinrude’s 60-horsepower model, it installed a water valve that injects water into the exhaust system, which changes the temperature of the medium and retunes the engine to perform better at a particular RPM, Sandstrom said.
Reduced weight, improved airflow
At Mercury, the majority of its two-stroke market is bass fisherman. In order to keep them on the water, enjoying their passion, the manufacturer focuses on reliability and fuel efficiency with reduced weight and improved performance.
In its 150-horsepower OptiMax Pro XS, Mercury installed carbon fiber reeds, which are more flexible and responsive than the stainless steel version they replaced. Along with a vented flywheel cover under the cowling, the result is improved airflow, leading to better performance.
“It is all about helping the engine breath better and improve combustion efficiency to gain higher torque and increased horsepower output,” Miller said.
Not your father’s two-stroke
Making digital throttle and shift systems and customizable interfaces possible, the computer behind the two-stroke outboard is also vital in controlling many of the segment’s pioneering technologies.
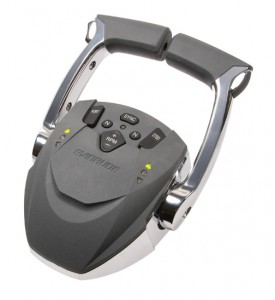
At Evinrude, the computer’s most important task is directing stratified combustion, which scales down the power of the engine when it is not necessary, such as when idling, for example. The result is a much more fuel-efficient event than homogeneous combustion, which the computer directs to kick in when necessary at full throttle.
Sandstrom said stratified combustion is a unique two-stroke feature that would be cost-prohibitive to its four-stroke competitors, which already have the added engine parts associated with the valve train.
And much like the advantages that are innate with four-stroke technology, these benefits are creatively exploited to gain an edge in the highly competitive world of outboard motors.
“Everyone out there building an outboard engine is building a quality product,” Sandstrom said. “You cannot be short on that aspect and make it in this market because consumers are too well educated and know exactly what they want.”
See sidebar within this article: The electric alternative